Automotive
Handheld Laser Welding VS Traditional Welding: A Comprehensive Comparison
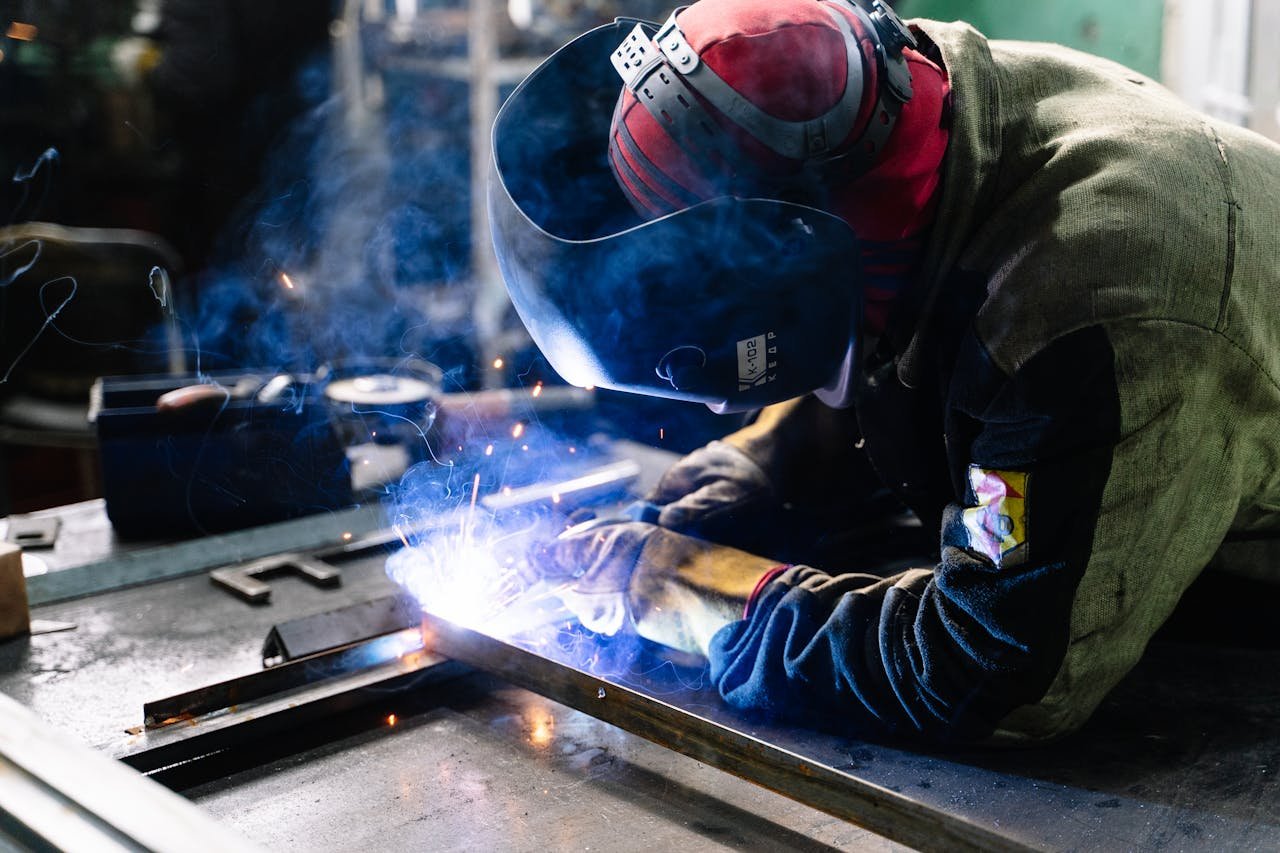
In the realm of metal fabrication, welding stands as a fundamental process for joining materials. Traditional welding methods have long been the norm. With advancements in technology, handheld laser welding has emerged as a viable alternative. Explore more of the differences between handheld laser welding and traditional welding techniques.
Understanding Traditional Welding
Traditional welding encompasses various techniques. These include arc welding, MIG welding, TIG welding, and spot welding. These methods involve using heat to melt and fuse metal pieces together. Welders often use handheld welding tools or welding machines to perform these tasks. They apply heat directly to the workpiece until a strong bond is achieved.
Exploring Handheld Laser Welding
Handheld laser welding represents a modern approach to joining metals. It utilizes a focused laser beam to create precise, high-quality welds. Traditional welding methods rely on heat from an electric arc or flame. However, laser welding generates heat through the concentrated energy of a laser beam. Welders can manipulate handheld laser welding devices to target specific areas with precision. This results in minimal distortion and excellent weld quality.
Advantages of Handheld Laser Welding
Handheld laser welding offers several advantages over traditional welding techniques:
Precision:
The focused nature of the laser beam allows for precise control over the welding process. This can enable welders to achieve accurate and consistent results.
Speed:
Handheld laser welding is generally faster than traditional welding methods. The laser beam melts the metal quickly and efficiently.
Minimal Heat Affected Zone (HAZ):
Laser welding produces a narrow heat-affected zone. It reduces the risk of distortion, warping, and material damage.
Versatility:
Handheld laser welding can be used on a wide range of materials. These include stainless steel, aluminum, and titanium, making it suitable for diverse applications.
Quality:
The high-energy density of the laser beam ensures strong, reliable welds with minimal porosity and defects.
Limitations of Handheld Laser Welding
While handheld laser welding offers numerous benefits, it also has some limitations to consider:
Cost:
Handheld laser welding equipment can be more expensive to purchase and maintain than traditional welding machines.
Skill Requirements:
Operating a handheld laser welding device requires specialized training and expertise. It involves working with high-powered laser systems.
Material Thickness:
Handheld laser welding may not be suitable for thick materials or highly reflective surfaces. It relies on the absorption of laser energy to create a weld.
Access:
Handheld laser welding may be challenging to perform in confined spaces or on complex geometries. This requires clear line-of-sight to the welding area.
Applications of Handheld Laser Welding
Handheld laser welding finds applications in various industries and sectors:
Automotive Manufacturing:
Handheld laser welding is used to join automotive components due to its precision and efficiency:
lbody panels
lexhaust systems
lchassis components
Aerospace Engineering:
In the aerospace industry, handheld laser welding is employed in the fabrication of aircraft structures, engine components, and fuel systems. The lightweight materials and high-quality welds are essential.
Electronics Production:
Handheld laser welding is utilized in electronics manufacturing. It is used for assembling components in smartphones, tablets, and other electronic devices. The precise, aesthetically pleasing welds are desired.
Medical Device Manufacturing:
Handheld laser welding is integral to the production of medical devices and instruments. These include surgical tools, implants, and prosthetics, where biocompatibility and precision are paramount.
Conclusion
Handheld laser welding represents a modern, efficient, and versatile approach to joining metals. It offers numerous advantages over traditional welding methods. It also has some limitations and challenges. But the benefits of precision, speed, and quality make it a valuable tool in various industries. As technology continues to advance, handheld laser welding is poised to become even more prevalent in the field of metal fabrication.
-
Business5 months ago
Sepatuindonesia.com | Best Online Store in Indonesia
-
Technology3 weeks ago
Top High Paying Affiliate Programs
-
Tech5 months ago
Automating Your Window Treatments: The Advantages of Auto Blinds
-
Tech5 months ago
Unleash Your Potential: How Mecha Headsets Improve Productivity and Focus
-
Instagram2 years ago
Free Instagram Follower Without Login
-
Reviews11 months ago
Android Laptop vs. Chromebook: Which one is better?
-
Instagram2 years ago
IGTOK – Get Instagram Followers, Likes & Comments
-
Business8 months ago
Follow These 5 Tips To Avail Personal Loans At Lower Interest Rates