Technology
Everything You Need to Know About Precision Wire EDM Machining
Whether you are an engineer looking for a precision machining solution or a manufacturer needing intricate metal parts, precision wire EDM
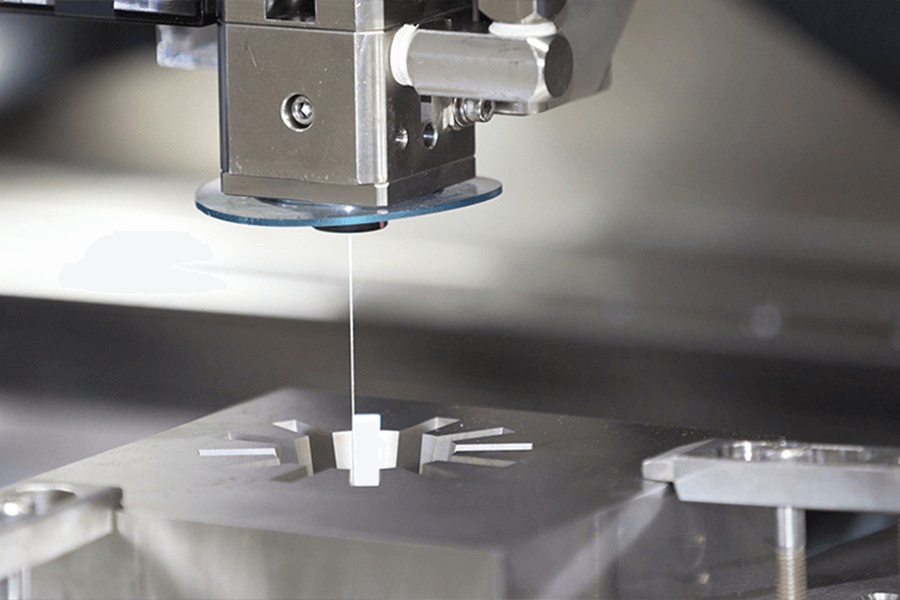
Whether you are an engineer looking for a precision machining solution or a manufacturer needing intricate metal parts, precision wire EDM is a technology you should explore. Wire electrical discharge machining (EDM) uses a continuously moving thin wire as an electrode to cut metal parts with exceptional accuracy. This CNC machining process has many advantages over traditional cutting methods, especially when tight tolerances and complex shapes are required.
What is Wire EDM?
Wire EDM, also known as wire-cut EDM, is a non-traditional machining method that involves no physical forces. Instead, it uses electrical sparks to erode metal piece by piece. A wire, typically made of copper or brass between 0.05-0.3mm in diameter, is fed through the workpiece which acts as an electrode. The wire is submerged in a tank of dielectric fluid and a precise electrical charge is applied between the wire and workpiece. This causes sparks to jump between the wire and workpiece, melting and evaporating tiny amounts of metal. By rapidly repeating this spark erosion thousands of times per second along a programmed path, highly accurate parts can be produced.
Key Benefits of Precision Wire EDM
There are several advantages that make wire EDM such a powerful precision machining solution:
- It can cut any electrically conductive material regardless of hardness, strength, or composition. Even advanced alloys that are difficult to machine can be cut with ease.
- Tolerances as tight as ±0.0004 inches or 0.01mm can be achieved. This level of precision is nearly impossible with traditional machining.
- Complex internal and external profiles can be produced thanks to the thin wire electrode. Undercuts, sharp corners, and intricate details are well within the capabilities of wire EDM.
- There is little mechanical force or heat introduced to the part during the machining process. This minimizes work hardening, deformation, and heat treatment issues common with other methods.
- Thin kerf widths of 0.004 inches or less allow for smaller features, closer spacing, and higher yields from raw stock.
Industries Benefiting from Precision Wire EDM
Given its strengths in machining advanced materials and creating complicated geometries with great accuracy, wire EDM flourishes across many industries including:
- Aerospace – Complex turbine blades, rocket engine components, airframe parts
- Automotive – Injection molds, DIES, manifolds, transmission components
- Medical – Surgical instruments, implants, prosthetics, dental tools
- Electronics – Connectors, sensors, semiconductors
- Firearms – Barrels, bolt components, small intricate parts
Custom Solutions from Experienced Suppliers
For engineers and manufacturers needing precision metal fabrication, it’s important to find an experienced wire EDM supplier. Companies like Zintilon have extensive capabilities and expertise in precision edm. They offer full customized machining solutions ranging from quick prototype production to high volume manufacturing. Engineers can upload 2D/3D CAD files and receive instant online quotes. Tight tolerances down to ±0.0004 inches, a variety of conductive materials, and short lead times are core strengths of top suppliers.
Tap into the Power of Precision Wire EDM
For any application requiring complex, close-tolerance metal parts machined from advanced alloys, wire EDM deserves serious consideration. Rather than being limited by material properties and part geometries, this flexible precision machining process thrives on challenging cuts. Connecting with a supplier that understands your requirements and can deliver timely, high quality solutions is key. Whether producing prototypes or assembling your next product line, the sparks of precision wire EDM could be exactly what your engineering or manufacturing needs.
Table of Contents
-
Business5 months ago
Sepatuindonesia.com | Best Online Store in Indonesia
-
Technology3 weeks ago
Top High Paying Affiliate Programs
-
Tech5 months ago
Automating Your Window Treatments: The Advantages of Auto Blinds
-
Tech5 months ago
Unleash Your Potential: How Mecha Headsets Improve Productivity and Focus
-
Instagram2 years ago
Free Instagram Follower Without Login
-
Reviews11 months ago
Android Laptop vs. Chromebook: Which one is better?
-
Instagram2 years ago
IGTOK – Get Instagram Followers, Likes & Comments
-
Business8 months ago
Follow These 5 Tips To Avail Personal Loans At Lower Interest Rates