Technology
Demystifying GD&T: A Beginner’s Guide to Geometric Dimensioning and Tolerancing
GD&T In the intricate world of engineering and manufacturing, precision is paramount.
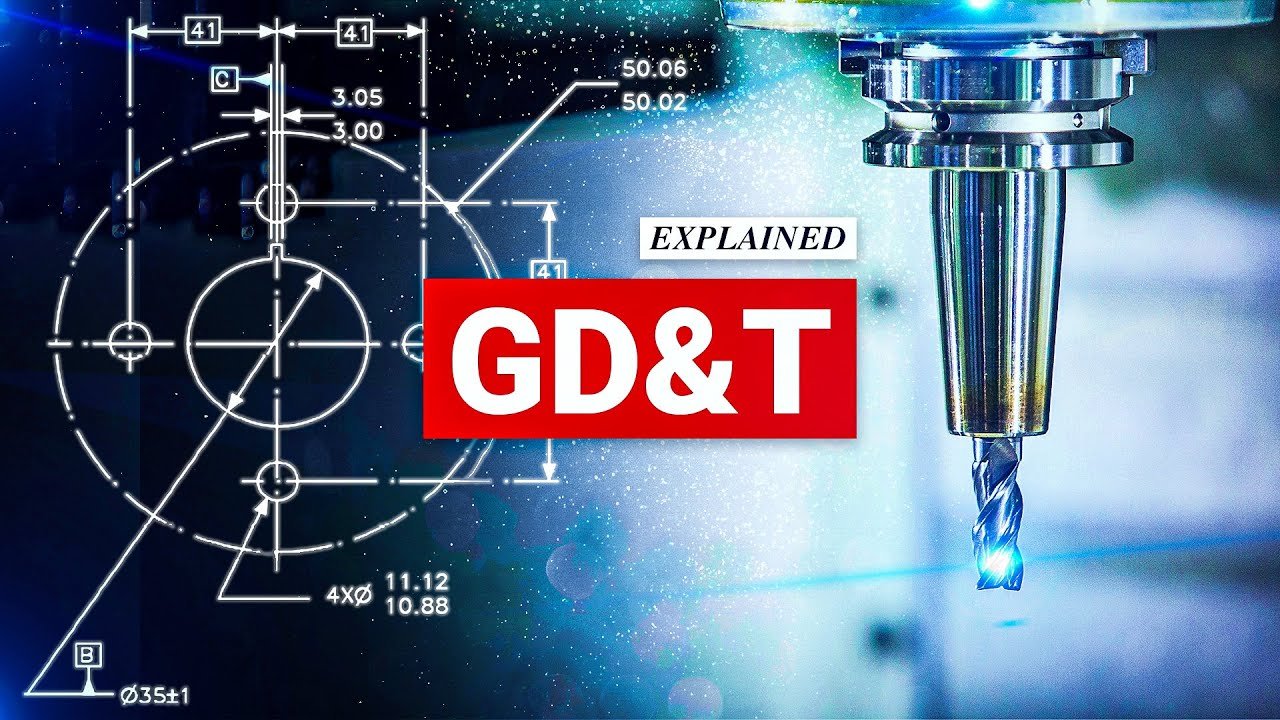
Introduction to GD&T
In the intricate world of engineering and manufacturing, precision is paramount. Every product, regardless of its scale, relies on meticulous design and exacting production to ensure functionality, reliability, and safety. Geometric Dimensioning and Tolerancing (GD&T) emerges as a vital tool in this pursuit. This guide aims to unravel the complexities of GD&T, providing beginners with a comprehensive understanding of its principles, applications, and benefits.
Defining GD&T
GD&T, short for Geometric Dimensioning and Tolerancing, serves as a symbolic language. It’s purpose? To communicate design specifications and tolerances for the geometry and dimensions of mechanical parts and assemblies. Unlike conventional linear dimensioning, which revolves around numerical values alone, GD&T offers a rich array of symbols and annotations. These symbols not only convey size but also encompass form, orientation, and location requirements. This holistic approach enables engineers, designers, manufacturers, and inspectors to communicate effectively, ensuring that parts adhere to specified dimensions and functions.
Tracing the Origins
The roots of GD&T delve into the early 20th century, coinciding with the rise of industrial standardization efforts aimed at enhancing manufacturing processes and product quality. However, GD&T solidified into a formal system for geometric dimensioning and tolerancing in the mid-20th century. The American Society of Mechanical Engineers (ASME) played a pivotal role in this evolution, with the publication of the ASME Y14.5 standard in 1994. This standard has since become the cornerstone of GD&T practices, not only in the United States but also across international borders.
Understanding the Fundamentals
To navigate the realm of GD&T, one must grasp its foundational concepts.
Deciphering Basic Symbols
At the heart of GD&T lies a comprehensive set of geometric symbols and annotations. These symbols delineate specific dimensional and geometric requirements. Among the crucial symbols are Straightness, Flatness, Circularity, Cylindricity, Profile of a Line/Profile of a Surface, Angularity, Parallelism, Perpendicularity, and Position. Each symbol serves to denote a different aspect of a part’s geometry or dimension, facilitating precise communication of design requirements.
Appreciating Datum Features
GD&T hinges on datum features, acting as reference points or planes from which dimensional and geometric tolerances emanate. Datum features lay the groundwork for the part’s coordinate system, ensuring consistent measurement and assembly. The selection of appropriate datum features is paramount, as it accurately defines the part’s geometry and fulfills the desired functional requirements.
Principles of Tolerancing
Tolerancing forms the bedrock of GD&T, enabling the specification of allowable deviations from nominal dimensions to accommodate variations in manufacturing processes.
Exploring Types of Tolerances
GD&T encapsulates five main types of tolerances: Form, Profile, Orientation, Location, and Runout. Form tolerances delineate the permissible variation in the shape of a feature, while Profile tolerances define the allowable variation of a feature’s shape or boundary within a specified tolerance zone. Orientation tolerances specify the permissible deviation of a feature’s orientation, whereas Location tolerances describe the allowable deviation in the position of a feature relative to a datum reference frame. Finally, Runout tolerances indicate the permissible variation in the circularity or total movement of a feature relative to a specified datum axis.
Establishing Tolerance Zones
Tolerance zones serve as the crux of GD&T, delineating permissible deviations from nominal dimensions. These zones set the acceptable boundaries within which a feature’s geometry or position must reside to meet design requirements. Tolerance limits, expressed as numerical values or percentages, define the maximum allowable deviation from the nominal dimension within the tolerance zone.
Benefits of GD&T
The adoption of GD&T heralds myriad advantages for engineers, manufacturers, and quality control professionals alike.
Facilitating Communication
By providing a standardized language for expressing design requirements, GD&T fosters clear and unambiguous communication across diverse stakeholders, including designers, engineers, manufacturers, and inspectors. This standardized approach mitigates the risk of misinterpretation, ensuring that everyone involved comprehends the desired specifications.
Enhancing Product Quality
GD&T engenders tighter control over dimensional and geometric variations, culminating in heightened product quality and consistency. By specifying tolerances with precision, manufacturers can produce parts that reliably meet functional requirements, thereby mitigating defects, rework, and scrap.
Understanding GD&T Symbols and Notations
A thorough comprehension of GD&T symbols and notations is imperative for interpreting engineering drawings and implementing design specifications accurately.
Unraveling Common Symbols
Let’s delve into some of the frequently encountered GD&T symbols and their denotations:
- Straightness: This symbol signifies that a feature must maintain straightness within a specified tolerance zone.
- Flatness: It dictates the allowable deviation from a perfectly flat surface.
- Circularity: It elucidates the permissible variation in the roundness of a feature.
- Cylindricity: This symbolizes the allowable deviation from a perfect cylindrical shape.
- Profile of a Line/Profile of a Surface: These symbols delineate the permissible deviation of a feature’s shape from its true profile.
Examining GD&T Callouts
Examples of GD&T callouts commonly feature in technical drawings, furnishing precise instructions for manufacturing and inspection processes. These callouts play a pivotal role in ensuring that parts conform to the specified requirements.
Applications of GD&T in Engineering Design
GD&T permeates every facet of engineering design, exerting influence over part manufacturing, assembly, and inspection processes.
Illustrative Engineering Design Examples
Let’s delve into two exemplary scenarios illustrating the practical application of GD&T in engineering design:
- Automotive Component Design: The automotive industry extensively employs GD&T to ascertain the precise fit and functionality of critical components such as engine blocks, transmission housings, and suspension components. By meticulously defining dimensional and geometric requirements, engineers optimize part designs to meet performance standards while minimizing production costs.
- Aerospace Machined Parts: In the aerospace domain, where safety and reliability are paramount, GD&T assumes a pivotal role in ensuring the dimensional accuracy and structural integrity of machined parts. Through the specification of tight tolerances and precise geometric requirements, engineers design components capable of withstanding the extreme conditions of flight while minimizing weight and material usage.
Challenges and Solutions
While GD&T proffers numerous benefits, its implementation is not devoid of challenges, especially for organizations new to the methodology.
Addressing Common Challenges
- Training and Education: Many engineers and technicians may lack the requisite training and expertise to interpret GD&T symbols accurately. Resolving this challenge necessitates investing in comprehensive training programs and furnishing ongoing education to ensure personnel proficiency in GD&T principles and practices.
- Software and Tools: The effective implementation of GD&T often mandates specialized software and tools for crafting, interpreting, and validating engineering drawings. However, selecting the appropriate software and ensuring compatibility with existing systems can prove daunting. Organizations must meticulously evaluate available options and invest in tools aligning with their specific needs and workflows.
- Cultural Resistance: Cultural resistance poses another obstacle to GD&T adoption, particularly in organizations entrenched in conventional practices. Overcoming this resistance demands robust leadership, effective communication, and an unwavering commitment to continuous improvement. By elucidating the benefits of GD&T and underscoring its impact on product quality and competitiveness, organizations can foster a culture conducive to innovation and collaboration.
GD&T Standards and Compliance
GD&T operates within a framework of industry standards and guidelines, ensuring uniformity and consistency in geometric dimensioning and tolerancing practices.
The ASME Y14.5 Standard
The American Society of Mechanical Engineers (ASME) Y14.5 standard stands as the cornerstone of GD&T practices, providing a comprehensive guide to geometric dimensioning and tolerancing. Initially published in 1994, this standard delineates uniform practices for expressing and interpreting geometric dimensioning requirements in engineering drawings. It covers an array of topics, including symbolic representation of geometric tolerances, datum feature selection and application, tolerance zone concepts and calculations, and dimensioning and tolerancing of features of size, form, orientation, and location.
International Standards
In addition to the ASME Y14.5 standard, the International Organization for Standardization (ISO) has developed a suite of standards pertaining to geometric dimensioning and tolerancing. These ISO standards furnish global guidelines for GD&T practices, ensuring harmonization across industries and regions. Key ISO standards include ISO 1101 for Geometrical product specifications (GPS) – Geometrical tolerancing – Tolerances of form, orientation, location, and run-out, ISO 5459 for GPS – Geometrical tolerancing – Datums and datum-systems for geometrical tolerances, and ISO 8015 for GPS – Fundamentals – Concepts, principles, and rules.
Adherence to GD&T standards is imperative for ensuring consistency, interoperability, and regulatory compliance across diverse industries and geographical boundaries.
GD&T in Manufacturing Processes
GD&T exerts a profound influence on manufacturing processes, shaping everything from part production to quality control and inspection.
Role of GD&T in CNC Machining
In computer numerical control (CNC) machining, GD&T serves as the linchpin for defining the dimensional and geometric requirements of machined parts. CNC machines leverage GD&T annotations to guide the machining process, ensuring that parts are manufactured to precise specifications with minimal deviation.
GD&T in 3D Printing
In the realm of additive manufacturing, or 3D printing, GD&T assumes paramount importance in specifying the dimensional accuracy and surface finish of printed parts. By incorporating GD&T annotations into 3D models, designers communicate precise geometric requirements to the printing equipment, thereby ensuring that printed parts adhere to the desired specifications.
Best Practices for GD&T Integration
To maximize the benefits of GD&T in manufacturing processes, organizations should embrace best practices:
- Early Integration: Incorporate GD&T considerations into the design phase to ensure that parts are manufacturable and meet functional requirements from inception. Early collaboration between design, engineering, and manufacturing teams is pivotal for identifying potential issues and optimizing part designs for efficient production.
- Standardization: Establish standardized GD&T practices and procedures across the organization to foster consistency and interoperability. This entails defining common datum reference frames, tolerance conventions, and inspection methodologies to streamline production and quality control processes.
- Training and Education: Provide comprehensive training and education programs to equip personnel with the knowledge and skills requisite for interpreting and applying GD&T effectively. Investing in employee development ensures that teams are proficient in GD&T principles and practices, mitigating errors and enhancing overall productivity.
- Continuous Improvement: Continuously review and refine GD&T practices based on feedback from manufacturing processes, inspection data, and customer requirements. Continuous improvement initiatives identify opportunities for optimization, ensuring that GD&T practices remain aligned with industry standards and best practices.
Training and Education in GD&T
Effective training and education constitute the bedrock for mastering GD&T principles and practices.
Learning Resources
A plethora of resources are available to aid individuals and organizations in learning GD&T:
- Textbooks and Reference Materials: Numerous textbooks and reference materials delve into GD&T, covering fundamental principles, symbol interpretation, and practical applications. Notable titles include “Geometric Dimensioning and Tolerancing” by David A. Madsen and “GD&T Application and Interpretation” by Bruce A. Wilson.
- Online Courses and Tutorials: Online platforms offer a myriad of GD&T courses and tutorials suitable for beginners and seasoned professionals alike. These courses typically feature video lectures, interactive exercises, and quizzes to reinforce learning objectives. Platforms such as Udemy, Coursera, and LinkedIn Learning host GD&T courses taught by industry experts.
- Professional Workshops and Seminars: Professional organizations and training providers organize workshops and seminars on GD&T topics, providing opportunities for hands-on learning, networking, and insights from industry experts. Organizations such as the American Society of Mechanical Engineers (ASME) and the Society of Manufacturing Engineers (SME) offer GD&T training programs and certification courses.
The Importance of GD&T Training
GD&T training is indispensable for engineers, designers, technicians, and quality control professionals involved in the design, manufacturing, and inspection of mechanical parts and assemblies. Training enables individuals to:
- Understand GD&T Principles: Develop a comprehensive understanding of GD&T symbols, notations, and concepts, enabling accurate interpretation and application in engineering drawings and specifications.
- Improve Communication: Enhance communication and collaboration between design,
- Ensure Compliance: Ensure compliance with industry standards and customer requirements by adhering to established GD&T practices and procedures. This includes correctly interpreting engineering drawings, selecting appropriate datum features, and applying tolerances in accordance with ASME Y14.5 or ISO standards.
- Optimize Manufacturing Processes: Identify opportunities to optimize manufacturing processes, reduce production costs, and improve product quality by applying GD&T principles effectively. This may involve refining part designs, selecting appropriate manufacturing methods, and implementing advanced inspection techniques to ensure dimensional accuracy and consistency.
Future Trends and Innovations in GD&T
As technology continues to advance, the field of GD&T is also evolving, with new trends and innovations shaping the way geometric dimensioning and tolerancing is applied in engineering and manufacturing.
Advancements in GD&T Software and Tools
One significant trend in GD&T is the development of advanced software and tools that streamline the creation, interpretation, and validation of GD&T annotations in engineering drawings and 3D models. Modern Computer-Aided Design (CAD) software packages offer robust GD&T capabilities, allowing designers to define and modify geometric tolerances with greater precision and efficiency. Integrated metrology software solutions enable seamless communication between design and inspection processes, facilitating faster and more accurate dimensional analysis.
Emerging Applications of GD&T in Industry 4.0
In the era of Industry 4.0, GD&T is playing an increasingly important role in digital manufacturing and smart production systems. The integration of GD&T with digital twin technologies enables real-time monitoring and control of manufacturing processes, ensuring that parts are produced within specified tolerances and quality standards. Advanced simulation tools leverage GD&T data to predict and optimize manufacturing outcomes, minimizing waste and maximizing efficiency. Augmented reality (AR) and virtual reality (VR) technologies offer immersive training experiences for GD&T education, allowing users to visualize and interact with complex geometric concepts in virtual environments.
Conclusion
Geometric Dimensioning and Tolerancing (GD&T) stands as a powerful tool for communicating design specifications and tolerances in engineering and manufacturing. By providing a standardized language for expressing dimensional and geometric requirements, GD&T facilitates clear communication, enhances product quality, and improves manufacturing efficiency. Mastery of GD&T principles and practices, coupled with effective training and education, is essential for harnessing its full potential in driving innovation, improving competitiveness, and delivering high-quality products in today’s dynamic marketplace.
As technology continues to advance, GD&T will play an increasingly critical role in shaping the future of design, manufacturing, and quality control. By embracing emerging trends and innovations, organizations can stay at the forefront of GD&T practices, ensuring continued success and growth in the ever-evolving landscape of engineering and manufacturing. Through continuous learning, adaptation, and collaboration, engineers, designers, and manufacturing professionals can unlock the full potential of GD&T to meet the challenges and opportunities of tomorrow.
Table of Contents
-
Business5 months ago
Sepatuindonesia.com | Best Online Store in Indonesia
-
Technology3 weeks ago
Top High Paying Affiliate Programs
-
Tech5 months ago
Automating Your Window Treatments: The Advantages of Auto Blinds
-
Tech5 months ago
Unleash Your Potential: How Mecha Headsets Improve Productivity and Focus
-
Instagram2 years ago
Free Instagram Follower Without Login
-
Reviews11 months ago
Android Laptop vs. Chromebook: Which one is better?
-
Instagram2 years ago
IGTOK – Get Instagram Followers, Likes & Comments
-
Business8 months ago
Follow These 5 Tips To Avail Personal Loans At Lower Interest Rates