Business
Unlock Ultimate Efficiency: 7 Essential Conveyor Maintenance Tools Every Factory Needs!
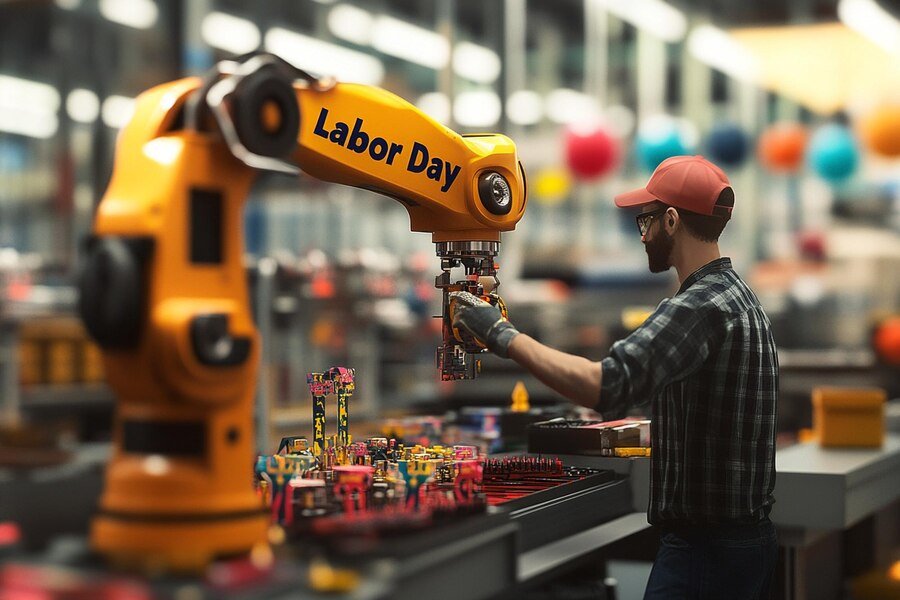
– Introduction: Importance of Conveyor Maintenance Tools
In the fast-paced world of manufacturing, conveyors serve as the lifelines that streamline workflows and enhance productivity. However, their efficiency hinges not only on robust design but also on consistent maintenance. This is where specialized conveyor maintenance tools come into play, transforming routine upkeep from a mundane task into a strategic advantage for factories aiming to maximize operational performance.
Essential Tool #1: Conveyor Belt Tension Gauge
A conveyor belt tension gauge is an indispensable tool that ensures your production line runs smoothly and efficiently. Maintaining the correct tension in a conveyor belt is critical; too loose, and you risk slippage or material misalignment; too tight, and you create unnecessary strain on the motor and rollers. By leveraging a tension gauge, factory managers can precisely monitor adjustments, prolonging equipment lifespan while minimizing unscheduled downtimes.
Essential Tool #2: Alignment Tools for Precision
Alignment tools are the unsung heroes of conveyor maintenance, crucial for ensuring operational precision and minimizing wear on components. A well-aligned conveyor system not only enhances performance but also extends the lifespan of your equipment, ultimately saving costs on repairs and downtime. Utilizing laser alignment tools can significantly enhance your precision in adjustments. These high-tech solutions provide real-time feedback, making it easier to identify misalignments that could lead to belt drift or inefficient operation.
Essential Tool #3: Lubrication Systems and Applicators
Lubrication systems and applicators play a crucial role in maintaining conveyor efficiency, often overlooked in the hustle of factory operations. By ensuring that every component runs smoothly and free from friction, these tools not only enhance the longevity of machinery but also minimize downtime—an essential factor in maximizing productivity. Advanced automated lubrication systems can be tailored to deliver precise amounts of lubricant at optimal intervals, addressing common wear areas on conveyors before they become problematic.
Essential Tool #4: Cleaning Equipment for Conveyors
When it comes to conveyor maintenance, the cleanliness of your system is often overlooked, yet it’s a crucial element that contributes to optimal performance. Cleaning equipment specifically designed for conveyors allows you to remove debris, dust, and contaminants that can accumulate over time. This not only helps in ensuring smooth operation but also prolongs the lifespan of critical components such as rollers and belts. Investing in specialized tools like rotary brushes or high-pressure air jets can make the cleaning process efficient and reduce downtime.
Imagine a cleaning routine that goes beyond surface-level tidiness; effective cleaning gear ensures that residue build-up doesn’t interfere with machinery function or product quality. By employing cutting-edge technologies such as FDA-approved sanitizers for food-grade applications, you address hygiene concerns while maintaining compliance with industry standards. Plus, scheduling regular cleanings with these tools fosters a culture of proactive maintenance rather than reactive fixes—a strategy that pays dividends through reduced wear and tear on your equipment. In an era where operational efficiency is paramount, prioritize cleaning equipment as part of your conveyor maintenance toolkit to elevate both productivity and reliability on the factory floor.
Essential Tool #5: Wear Measurement Instruments
When it comes to conveyor maintenance, wear measurement instruments are often the unsung heroes of operational efficiency. These tools allow factory managers to gain precise insights into the condition of critical components like rollers and belts, effectively acting as a diagnostic tool for potential failure points. With the ability to measure wear at micrometer levels, these instruments help in identifying anomalies before they escalate into costly repairs or production downtime.
Essential Tool #6: Vibration Analysis Tools
Vibration analysis tools are a game-changer in conveyor maintenance, unlocking a wealth of insights that go beyond mere visual inspections. These state-of-the-art devices measure vibrations at various points along the conveyor system, offering real-time data on mechanical health. By identifying abnormal vibration patterns, maintenance teams can proactively address issues such as misalignment or bearing wear before they escalate into costly breakdowns.
Essential Tool #7: Safety Gear and Accessories
When it comes to conveyor maintenance, safety gear and accessories are non-negotiable elements that safeguard not just your workforce but also the seamless operation of your equipment. Proper personal protective equipment (PPE) such as gloves, safety glasses, and helmets should be standard fare in every factory setting. However, embracing a broader range of safety accessories can elevate protection to new heights. Consider reflective vests for visibility in busy environments or knee pads designed for technicians who frequently kneel while inspecting machinery—these small adjustments can significantly enhance comfort and efficiency.
-
Business1 year ago
Sepatuindonesia.com | Best Online Store in Indonesia
-
Tech5 months ago
How to Use a Temporary Number for WhatsApp
-
Technology9 months ago
Top High Paying Affiliate Programs
-
Tech4 weeks ago
Understanding thejavasea.me Leaks Aio-TLP: A Comprehensive Guide
-
Technology5 months ago
Leverage Background Removal Tools to Create Eye-catching Videos
-
Social Media8 months ago
The Best Methods to Download TikTok Videos Using SnapTik
-
Instagram3 years ago
Free Instagram Follower Without Login
-
Instagram3 years ago
Free Instagram Auto Follower Without Login