Technology
5 Key Benefits of Using CNC Metal Parts in Industrial Applications
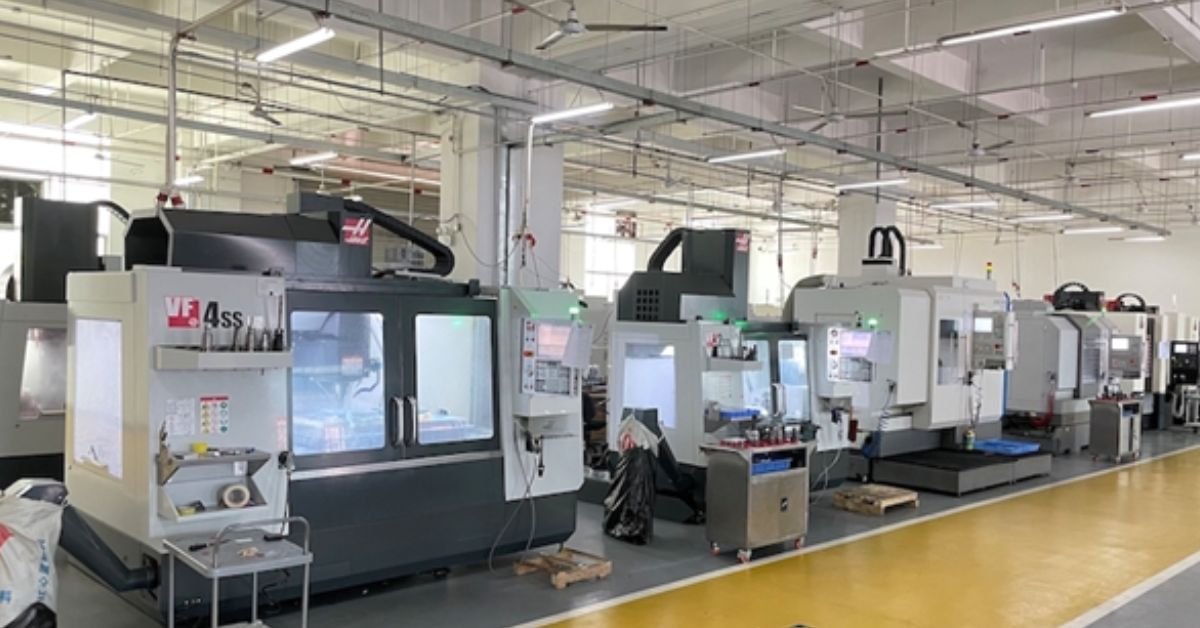
CNC machining has revolutionized the landscape of industrial manufacturing, particularly in the realm of metal fabrication. As industries evolve and demand more sophisticated and precise components, CNC metal parts have become indispensable. These parts are crafted through a process that integrates computer numerical control (CNC) with traditional metalworking techniques, resulting in components that offer unmatched precision, consistency, and efficiency.
In this article, we explore the key benefits of using CNC metal parts in industrial applications, showcasing how this technology enhances productivity and drives innovation in manufacturing.
1. Precision and Accuracy
One of the most significant advantages of using CNC metal parts in industrial applications is the unparalleled precision and accuracy they provide. In industries where even the smallest deviations can lead to significant issues, CNC machining ensures that each part is produced to exact specifications. The computerized nature of CNC machines allows for precise control over all aspects of the manufacturing process, from cutting and drilling to shaping and finishing.
The accuracy of CNC machining is particularly beneficial in industries such as aerospace, automotive, and medical device manufacturing, where components must meet stringent tolerances. With CNC metal parts, manufacturers can achieve a level of precision that manual processes simply cannot match. This precision not only enhances the quality of the final product but also reduces the need for post-production modifications and adjustments, saving both time and resources.
2. Efficiency and Productivity
Efficiency is a critical factor in industrial manufacturing, and CNC metal parts significantly contribute to improving productivity across various applications. CNC machines are capable of operating continuously with minimal human intervention, which translates to faster production times and higher output rates. Unlike traditional machining methods, which require skilled operators to manually guide the tools, CNC machines execute pre-programmed instructions with consistent speed and accuracy.
This automation reduces the likelihood of errors, further enhancing productivity by minimizing rework and scrap. The ability to run CNC machines around the clock without fatigue allows manufacturers to meet tight deadlines and increase production capacity. The efficiency gained from using CNC metal parts ultimately leads to cost savings, as manufacturers can produce more parts in less time, all while maintaining high standards of quality.
3. Complexity and Customization
Another notable benefit of CNC metal parts is their ability to accommodate complex geometries and custom designs. Traditional machining methods often struggle with intricate designs, especially when producing parts with tight tolerances or unconventional shapes.
Manufacturers can easily create custom CNC metal parts that meet specific requirements, whether for prototyping or full-scale production. This flexibility is particularly valuable in industries that require unique or highly specialized components, such as medical devices or custom machinery. By using CNC machining, manufacturers can efficiently produce small batches of customized parts without compromising on quality or precision.
CNC machining allows for the rapid prototyping of new designs, enabling engineers to test and refine their concepts before moving to mass production. This iterative process is essential for innovation, as it reduces the time and cost associated with developing new products. Companies like WayKen, a leader in CNC machining services, have made significant strides in providing customized solutions that cater to the evolving needs of various industries.
4. Consistency and Repeatability
Consistency is a key requirement in industrial manufacturing, particularly when producing large volumes of identical parts. CNC metal parts offer a level of repeatability that manual processes cannot achieve. Once a CNC machine is programmed to produce a part, it can replicate that part with the same level of precision every time, regardless of the quantity.
This consistency is crucial in industries where components must fit together perfectly or perform reliably under demanding conditions. For example, in the automotive industry, where thousands of identical parts are needed for vehicle assembly, CNC metal parts ensure that each piece meets the required specifications. This repeatability not only improves the quality of the final product but also simplifies the assembly process, reducing the risk of defects and ensuring that the end product performs as intended.
Furthermore, the use of CNC metal parts helps maintain quality control throughout the production process. By minimizing variability, manufacturers can ensure that their products meet industry standards and customer expectations, leading to greater customer satisfaction and brand loyalty.
5. Cost-Effectiveness
While the initial investment in CNC machinery and programming may be significant, the long-term cost benefits of using CNC metal parts are substantial. One of the primary cost advantages is the reduction in labor costs. CNC machines require less manual intervention, allowing manufacturers to allocate their workforce more efficiently. This not only lowers labor costs but also reduces the risk of human error, which can lead to costly rework or scrap.
CNC metal parts contribute to cost-effectiveness by reducing material waste. CNC machines are programmed to optimize the use of raw materials, cutting only what is necessary to produce the desired part. This precision minimizes waste and ensures that manufacturers get the most out of their materials, ultimately reducing production costs.
The durability and reliability of CNC metal parts lead to fewer maintenance issues and longer equipment lifespans. Since CNC machines produce parts with high accuracy and consistency, the likelihood of defects is significantly lower, resulting in fewer returns or replacements. This reliability translates to cost savings over time, as manufacturers spend less on repairs and downtime.
WayKen, known for its expertise in CNC machining, has demonstrated how these cost-saving benefits can be realized in various industries. By leveraging advanced CNC technology, companies can achieve a competitive edge through reduced production costs and improved product quality.
Conclusion
The precision and accuracy of CNC metal parts ensure that manufacturers can meet the most stringent tolerances, while the efficiency and productivity of CNC machines enable faster production times and higher output rates. The ability to create complex and customized parts allows for greater innovation and flexibility, while the consistency and repeatability of CNC machining ensure that every part meets the same high standards.
As CNC technology continues to advance, the benefits of using CNC metal parts in industrial applications will only become more pronounced, driving further innovation and efficiency in manufacturing. Whether you are looking to improve precision, boost productivity, or reduce costs, CNC metal parts offer a powerful solution that can help your business stay competitive in a rapidly changing industrial landscape.
-
Business9 months ago
Sepatuindonesia.com | Best Online Store in Indonesia
-
Technology5 months ago
Top High Paying Affiliate Programs
-
Tech48 minutes ago
Understanding thejavasea.me Leaks Aio-TLP: A Comprehensive Guide
-
Tech9 months ago
Automating Your Window Treatments: The Advantages of Auto Blinds
-
Tech9 months ago
Unleash Your Potential: How Mecha Headsets Improve Productivity and Focus
-
Instagram2 years ago
Free Instagram Follower Without Login
-
Instagram2 years ago
Free Instagram Auto Follower Without Login
-
Business12 months ago
Follow These 5 Tips To Avail Personal Loans At Lower Interest Rates